The increasing capacity puts pressure on innovation which allows for a gain in efficiency on last mile operations. Referring to the definition, the capacity of the last mile has direct influence of economic spheres of the process. This chapter shows three innovative solutions for the different phases of development, that is: longer and/or heavier vehicles (LHV) are a solution partially in use with developmental advantages in all BSR countries. Trucks platooning and autonomous trucks are technologies where the first tests in Europe already are arranged. However, these two technological innovations are still not widely used in the market.
7.2.1 LHV Trucks
LHV Trucks in LM operations have risen from the development of EMS Technology widely used in Scandinavian countries starting from 1980s. The constant development and research on LHV led the market providing solutions suitable for LHV-use as the last leg for CT operations. Such development included the building fleet of container or swap body trailers, dollies, or B-double suitable for transporting ILU.
In fact, the current status of the modular system and access of LHV is not homogenous in all Member States. The status quo for maximum allowed vehicle parameters in the EU is indicated in the Directive 96/53. It gives allowance to work on 40 tonnes of Permissible Laden Mass (i.e., 44 tonnes for intermodal traffic) with a length of 18.75 m) (Council Directive 96/53/EC, 1996).
Presently, trucks longer or heavier than the indicated Directive 96/53 are accepted on roads in Finland, Sweden, Denmark, and Germany. Conditions of LHV carriage and maximum allowed parameters differ for each particular Member State. The BSR is divided into northwest—where LHV are allowed or are currently under trial (Table 7.1)—and southeast—where the limits are still set according to Directive 96/53.
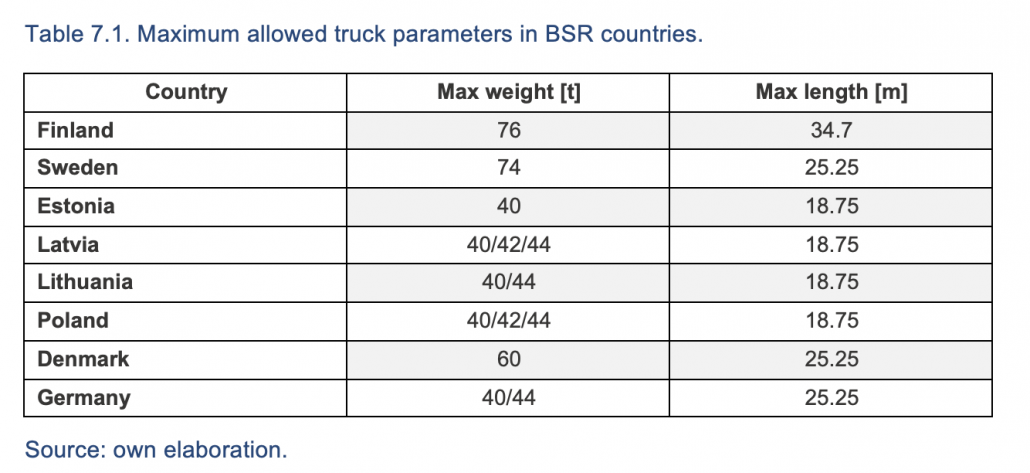
In general understanding LHV refers to trucks 25.25 m or longer developed in Scandinavia. In this e-book, to better understand specific BSR market conditions, the LHV definition will include also truck combinations which do not exceed the length but give the possibility to extend laden mass only.
LHV equipment
In order to meet legal requirements for the maximum weight of trucks, length or axle loads vehicle manufacturers prepare a sort of equipment used in CT in Europe. Currently, there are four main ways to build LHV according to EU legal requirements (Figure 7.2).
Base vehicles for most LHV, similar as for the standard configurations are tractor units. To meet legal requirements regarding CT operations and permissible axle loads, tractors used in LHV need to be equipped in three axles. Such units with a variety of engines and cabs are in portfolios of most truck manufacturers in Europe and BSR. Trucking companies can choose between 420-760 HP diesel engines but, lately, many manufacturers also offer LNG or CNG propelled units—with the near future looking at full plug in electric trucks. According to test runs recently conducted in Sweden, also fully electric trucks can serve the last mile up to 150km one way in 60 tonnes LHV truck configuration (Volvo Trucks, 2021).
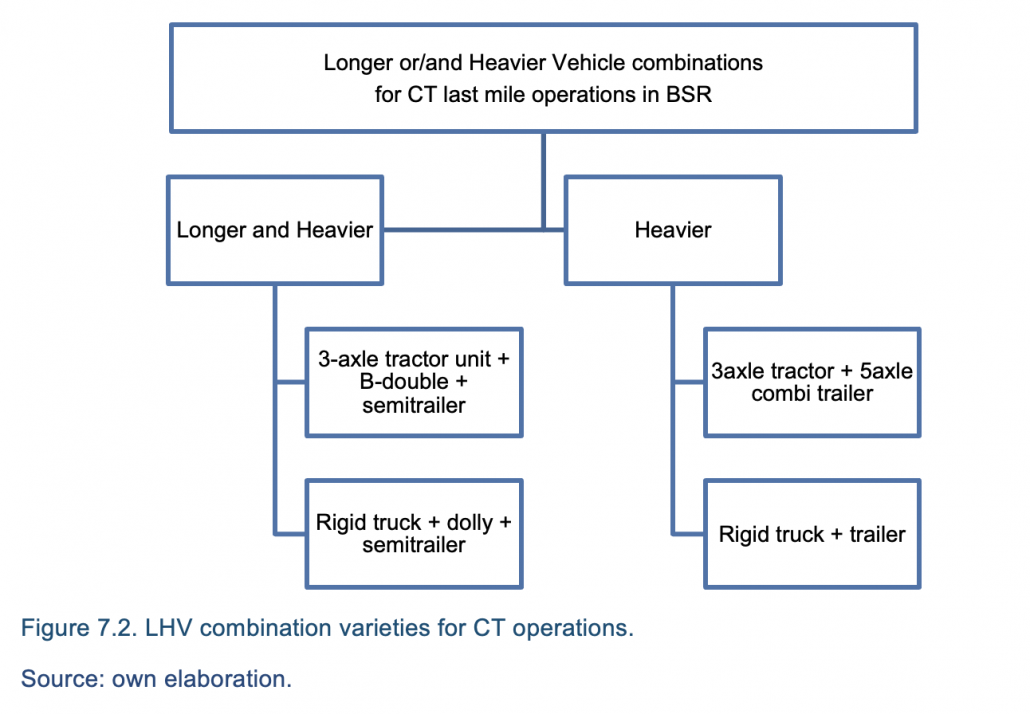
Heavier truck combinations
A number of ILUs transported in CT are considered as heavy units. This refers mainly to units of 20’ containers which can be transported on trailers in two-unit combinations without exceeding the maximum length. Unfortunately, combining ILUs to utilize the maximum capacity of a truck, in terms of TEU capacity and weight, is complicated and limited to current workflow on last mile operations. This is the basis for the development of combi trailers. Combi trailers are a solution developed in the Netherlands by manufacturers such as D-Tec (Figure 7.3) and Broshuis. The trailer consists of two modules which can work as separate trailers or as one vehicle. Thanks to an additional two axles of the combination, trailers are combined with a 3-axle tractor unit which can transport heavier units with a total capacity of 2 TEUs.
Higher permissible weight is not the only advantage of combi trailers. For CT operations, cargo discharging time is one of the crucial performance factors. Thus, the possibility of detaching one container for the stripping process and transferring it from one container to another location allows for valuable time management. In this place, it has to be noticed that second-hand market led the BSR trucking companies to equip the fleet in combi trailer units. It is widely visible on roads in Poland, where combi-trailers became a popular solution for lots of container trucking companies, despite lack of legal framework prepared for such technology.
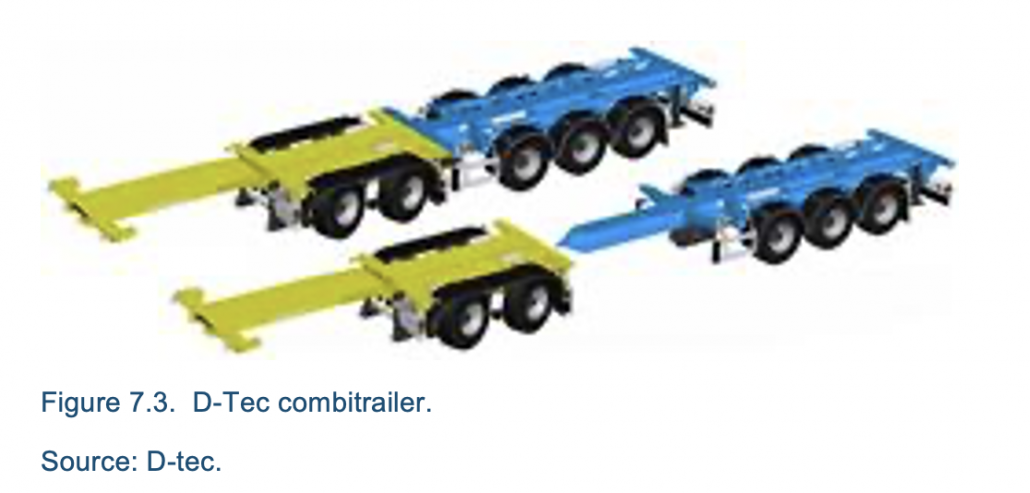
Longer and heavier vehicles
Longer and heavier trucks up to 25.25 m can be built up based on tractor unit or rigid truck. Both options can apply 3 TEU capacity, but in countries which allows LHV traffic the most popular is the tractor unit configuration. In this configuration, three TEU capacity is allowed due to equipment use called B-double. It allows for the load of one TEU directly on the tractor’s fifth wheel. The additional fifth wheel allows to attach any kind of semitrailer and, if needed, a 5-axle combi trailer with 2 TEU capacity. Such trailer combinations are available on Scandinavian and Benelux markets – where manufacturers such as VAK, Broshuis, and D-Tec supply the market. To this point, South Baltic markets are still a niche for those companies. As soon as LHV trucks will be launched on South Baltic regional roads, it will push the development of vendors and relating service network. A question on the real limitations of launching LHV still remains.
LHV launching limitations
A number of expert interviews and desk research led to indicate general topics to be resolved before launching LHV in whole BSR market.
Maximum axle loads
Truckers involved in CT last mile operations are not always aware of the cargo distribution inside the ITU. Most of the newbuild container chassis are equipped with the axle weight balancing systems, but we still have to remember that ILU also means intermodal trailers which mostly are not equipped in such solutions. This cause the needs to develop the CT terminals infrastructure to avoid overweight trucks across the last mile operations. On the other hand, for example, in Poland there are a varieties of axle load limitations on public roads. Depending on the ownership of the road (i.e., national, municipal) axle loads can vary from 11.5 through 10 up to 8 tonnes per axle. This indicates the need to create coherent network of infrastructure suitable for LHV trucks.
Road sections availability, parking infrastructure, distribution centers
Launching LHV requires proper infrastructure works not only on the roads and intersections. LHV will require retrofitting parking lots and building infrastructure required for coupling and maneuvering inside terminals and distribution centers.
Vehicle registrations
B-doubles, dollies and combi-trailers are special equipment which requires to be mentioned in legal framework. In some countries i.e., Poland based on current legal framework it is restricted to combine three-module vehicles, so proper legal works to create coherent market for LHV are a must.
Society and transport market effects
The lack of information about the technology can let the citizenry to create false image on LHV trucks safety. Tests conducted in the past prove that LVH in many aspects were safer on the road than standard trucks. For example, braking performance in LHV due to more axles can be higher than in standard trucks. First, longer combination leads to improving the road safety though a smaller number of vehicles used to carry the same payload.
On the other hand, risen maximum permissible mass can be boosted to unfair competition—market-wise. Technically LVH equipment can bear the cargo weight up to 80 tonnes and it can be used by some entrepreneurs to overweight their trucks.
Economic backgrounds of launching LHV
Within the scope of COMBINE project Report 4.1, the University of Gdansk in cooperation with the forwarding company conducted a trial test of LHV truck in the Polish market. For a one week a tractor unit with combi-trailer performed a number of last mile deliveries of 2×20’ containers with raw material for a factory located 120 km away from CT terminal.
Trial runs showed that using combi trailers can led to decrease unit costs even up to 30% in comparison to using standard tractor units with semi-trailers (Figure 7.4).
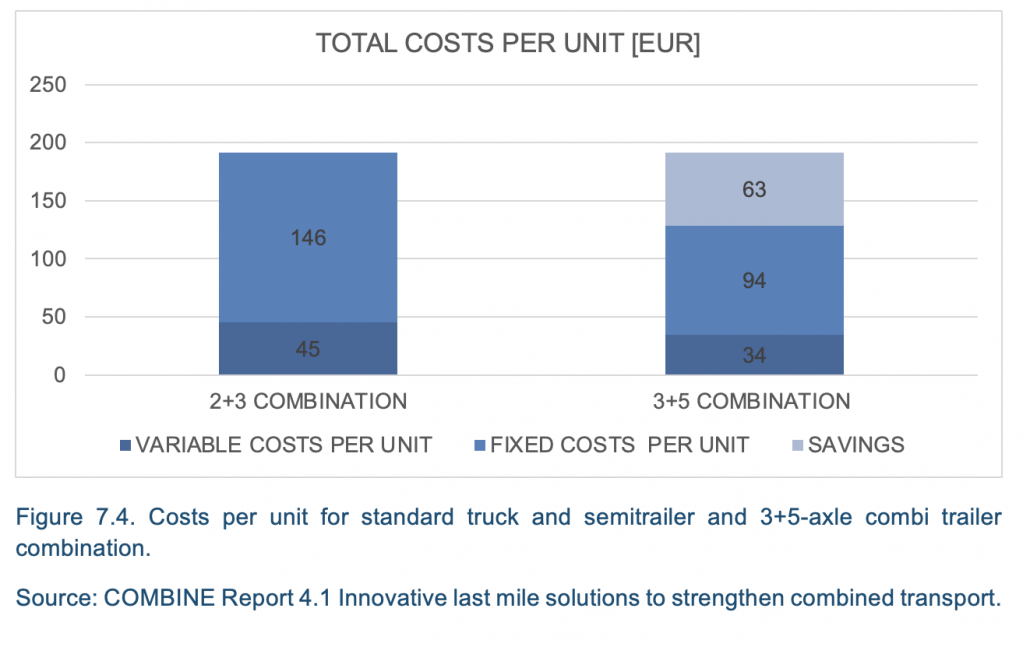
Trucks platooning
Trucks platooning technology allows to connect the trucks into a convoy with small distances in-between. This to reduce space-use on roads and to decrease the wind resistance by promises on reduced fuel consumption. Communication between vehicles (v2v) allows to follow the first leading vehicle and in the future development to release driver’s attention.
Development on platooning technology is divided into four stages, starting from only longitude control on vehicles, through an increased automated transport process with diver’s reaction needed in critic situation up to introduction of fully autonomous vehicles (Table 7.2).
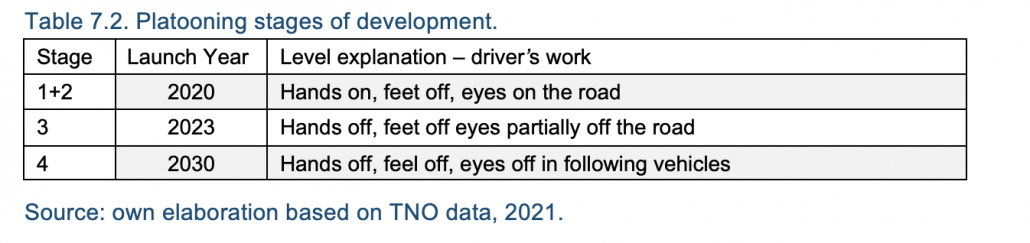
7.2.2 Economic calculation for BSR market
Trucks platooning technology for now is not widely available on the market, so the price only can be estimated based on prearranged tests. TNO report estimated cost of equipment needed for truck platooning on EUR 12,000 for first stage, for third EUR 16,000, and fourth for EUR 20,000 (TNO, 2017).
Such an investment requires a proper investment return rate. Platooning can provide economic savings mainly due to decreased fuel consumption but also in next stages of development—labor costs savings (Table 7.3).
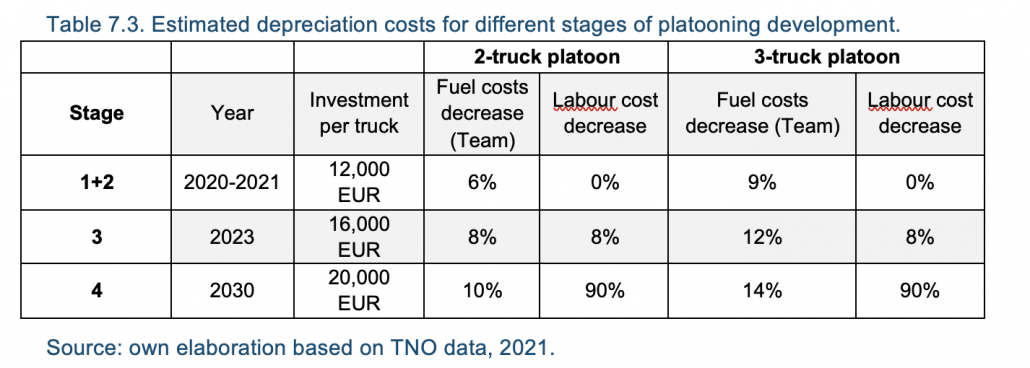
Setting together 1+2 stage estimations into the BSR market, it can be said that the following assumptions can apply:
- average diesel consumption 35l/100 km;
- costs of technology: EUR 12,000 / truck;
- average diesel price EUR 1.10, max EUR 1.30, min EUR 0.93, and EUR 1.50 as a reference;
- average monthly mileage per truck in CT last mile operations may vary between 4,000 and 7,000 km depending on factors like: distances, awaiting time, traffic conditions etc.; and
- depreciation time for trucks is set on 60 months (5 years).
Two trucks platooning gains the efficiency of investment after braking 7,000 km mileage per month of driving. Such mileage levels are possible to gain only in heavy, long distance road haulage, not in CT operations; hence, for BSR is necessary to consider platoons with three trucks coupled (Figure 7.5).
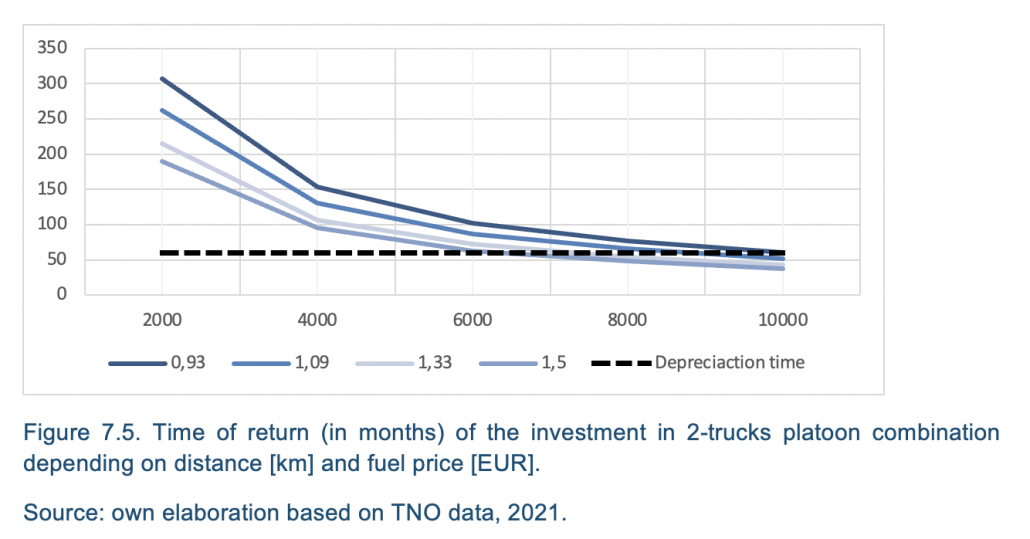
Extending the platoon for another truck moves the investment efficiency point at the level of approx. 5,000-6,000 km per month, depending on real fuel prices (Figure 7.6).
Another level of platooning development allows to receive further costs decrease closely connected not only with fuel consumption, but also with labor costs. In the fourth phase of technology development, platoons might be able to give up to 90% costs decrease of labor which refers to 20-25% of total costs of truck ownership. Different studies estimate, that the last stage of truck platooning development may lead to decrease of ownership cost by 55% (W. Schildorfer, 2019).
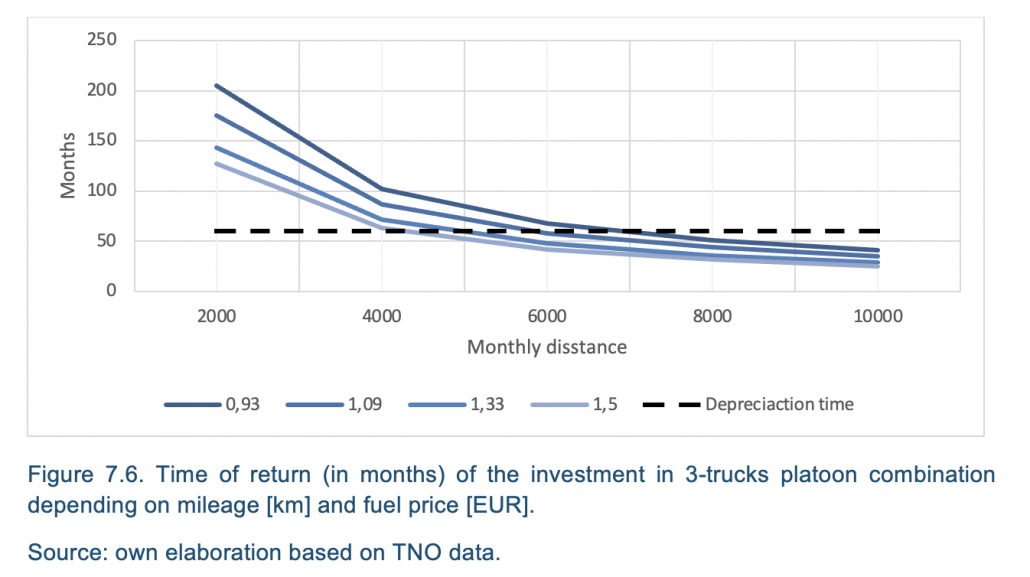
7.2.3 Business Case—suitability for BSR
A well-developed and legally introduced innovation means nothing when it’s unusable in practice. The point is to outline the business environment where platooning can be successfully implemented.
Close connection to Highways
Truck platoons are expected to be allowed on highways and expressways. Also, its value case remains valid if the technology can be used as often as possible. Thus, investment in truck platoons makes sense only for last mile deliveries from/to terminals situated nearby such roads. By analyzing the localization of CT terminals in the BSR – some of the terminals do not have direct access to motorway, nor any kilometer within the vicinity of the terminal based on a 20-50 km radius (see Malaszewicze terminals, Poland).
Proper cargo at proper time and place
Pairing the trucks into platoons during CT last mile operations requires to move ILUs at one time into the same time or as much as possible a similar destination. This requirement actually may have negative influence on CT. Combined transport is often considered as a solution to create a “rolling warehouse”. That is, ILUs stored at a terminal can be flexibly delivered at a destination due to its close location. Trucks platooning limits this flexibility of delivery time as trucks in platoon will deliver a number of ILUs at once. Secondly, last mile operations time is of crucial importance. On the one hand, platooning in its third stage of development will allow the extension of driver’s daily working time. On the other, waiting for the possibility to create platooning might overcome the potential savings in drivers operational working time.
Based on above conditions an individual studies should be conducted to analyze the flow of last mile traffic from terminals in order to give a real potential of platooning for CT operations. In all probability, platooning can be a proper and efficient solution only for particular supply chains in CT operations.
Distance
As it was mentioned, the distance of last mile deliveries is limited in the legal framework. Limitation is set on the nearest suitable station or to the radius 150 km from seaport/ CT terminal. The largest profits in terms of platooning is available on long(er) distances, with the high share of motorways in the voyage. Also, the length of road has the influence on the possibility to successful platooning. In CT operation chance for platooning is possible mainly for traffic to/from the terminal.
Market fragmentation
Last mile deliveries are conducted in a variety of business models, depending on the country, local markets, and specific agreement between involved stakeholders. Last mile operations can be arranged by self-employed operators, transport subcontractors, or CT operator’s owned trucking fleet. Such fragmentation builds upon the obstacles and innovation to create a coherent platooning network. The ENSEMBLE project will provide the solution to build upon a common interface for different truck manufacturers. Technology and ability are the first case, the second case is the proper planning to concentrate the stakeholders. This would be possible with proper software which automatically notifies interested parties about the possibilities of platooning within CT last mile.
7.2.4 Autonomous Vehicles
The next step to last mile technologies development is to introduce fully autonomous vehicles. This technology was first commercially tested by Volvo in 2019. The Swedish manufacturer tested a vehicle called Vera in container transport operations in Gothenburg.
Tests in commercial operations were conducted also by the company Einride. Those were taken in the terminal of Schenker in Jonkoping, Sweden. The special permission allowed for testing on public road with a max speed of 5 km/h. T-Pod truck had a maximum capacity of 20 tonnes and a battery allowance to drive a maximum of 200 km on one charge. The first test of Einride autonomous trucks in use under container transport operations are planned in the port of Helisngborg, SE. Einride as one of the first autonomous trucks manufacturers provided commercial price of the T-Pod truck which is estimated at USD 150,000 (40ton.net, 2018).
How can autonomous vehicles approach commercial last mile operations in BSR? Observing the very first tests where autonomous trucks were applied, terminals with a nearby location to the logistics or distribution centers is a start.
Access of autonomous trucks on public roads requires a lot of legal work in which is similar to tuck platooning. Thus, it seems, such vehicles will require additional infrastructure like internal roads or paths between terminals and nearby warehouses or distribution centers to allow for them to work—despite legal issues on public roads. Example terminals which might easily access such vehicles include: CLIP terminal Swarzędz – with its close location to distribution park CLIP II or DCT Gdansk.
New innovation in technology may also lead to the rise of an innovative market structure. Autonomous vehicles will need providers of IT solutions, controllers, and maintenance services. Such services can be offered by manufacturers directly or with the outsourced subcontractors which can become a new part of Last Mile solutions market.
7.2.5 Summary and recommendations
LHV trucks are the easiest way to improve the efficiency on last mile CT operations. BSR region is divided into northwest where LHV technology is legally allowed, and southeast where only trucks in EC directive parameters are allowed. This leads the BSR region countries to work on coherent network of LHV allowed countries.
Within the scope of biggest limitation of LHV has to be indicated the need of infrastructure retrofitting. As most of the newbuild roads in BSR are suitable for heavy traffic, the biggest infrastructure works should take place on the distribution centers and parking lots. Longer vehicles needs extra place for parking, coupling and maneuvering, so works on point infrastructure is a must. Indicating the proper linear infrastructure can take place based on best practices from Western BSR. As the good example can be the “PositiveNetz” in Germany—a clear network of roads where longer and heavier vehicles are allowed.
The next step required to setup the LHV in whole BSR is to regulate the legal base for registration of vehicles. The models required for such traffic like b-double or even combi trailers are not regulated in national or EU level legal framework. Despite that, transport market overtakes the legal works, and trucking entrepreneurs are already equipped in proper equipment (Figure 7.7).
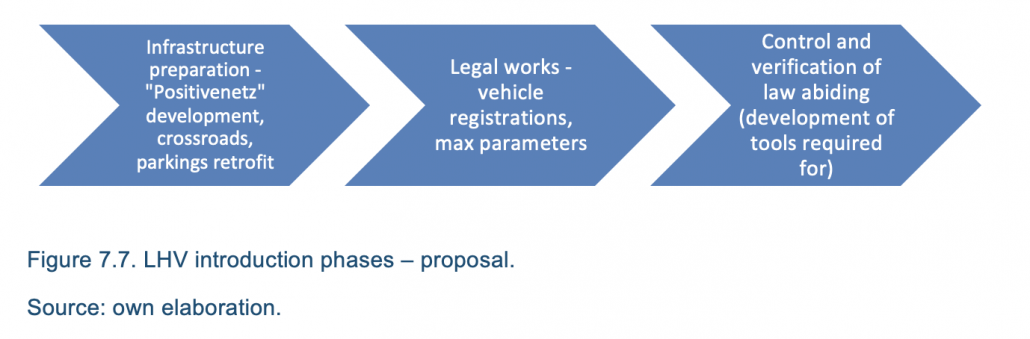
Legal regulations and infrastructure retrofit will not be enough for proper market functioning. Increasing maximum truck weight may lead to unfair competition and abusing the law by overweighting the LHV. Thus, proper market regulation and penalties for companies which abusing the law will be a must. The verification of a proper execution of LHV development may be conducted by variety of new technologies including GPS and geofencing which allows to constantly control the traffic flow.
Trucks platooning is an innovative technology which may not be widely introduced on CT last mile market. Research conducted within the scope of COMBINE 4.1 Report showed that based on current available technology costs it may be suitable only for a very short number of CT operations. Despite its increasing capacity function truck platoons makes economic sense only under specific conditions which seriously limits its usability in BSR. Thus, future development or investments in truck platooning technology in BSR has to be preceded by feasibility studies and CT traffic research to make sure if platooning will be usable in particular business environment.
The next step after trucks platooning leads the last mile operations to autonomous vehicles. Market research showed that the technology is on an advanced tests level. Although, its wide introduction to the market can be held by a legal works required to launch the technology on public roads. In real CT operations environment autonomous vehicles can be easily introduced on CT facilities with distribution centers or warehouses in its surroundings. This may lead to the preparation of internal paths or roads for autonomous vehicles to be in use before launching on public roads with proper legal framework.